In-Track Flash-Butt Welding
Holland is the industry leader in the field of flash-butt welding, not only in terms of available resources but also in experience and dedication to continual development of new technology that enables us to adapt to the evolving requirements of the railroad community. In 1972, Holland unveiled the first self-propelled railcar with a portable electric flash-butt welding machine in North America. Today, our fleet is the largest in the world with over 200 MobileWelders® across North America and Australia as well as flash-butt welding equipment operating in over 36 countries.
Our Intelliweld® Control System provides an unmatched degree of accuracy and quality in the production of rail welds. We pride ourselves as pioneers in developing flash-butt welding technology that continues to provide high-quality and cost-effective solutions. As we continue to innovate welding solutions, we apply our industry-leading technology and expertise across a variety of applications.
Simple program adjustments allow us to tailor rail consumption to your requirements for localized track structures & target rail-neutral temperature. Lower rail consumption reduces the amount of de-clipping and clipping required, improving productivity and reducing labor costs.
Features of this system
- Single system control
- Hardened electronic equipment
- Remote welder interface for software updates and troubleshooting
- Certified weld schedule lock
- Sub millisecond weld process control
- Flashing interrupt monitoring
- In process automated weld parameter adjustment
- Automated calibration routine
- Valve null readings determined during calibration
- Automated weld quality checks
Flash-butt welding provides a number of benefits over thermite welding such as faster installation, reduced maintenance costs, and a stronger joint with consistent hardness. Learn more about the Benefits of Holland’s Flash-butt Welding Versus Thermite Welding.
EXPLORE OUR WELDING SOLUTIONS
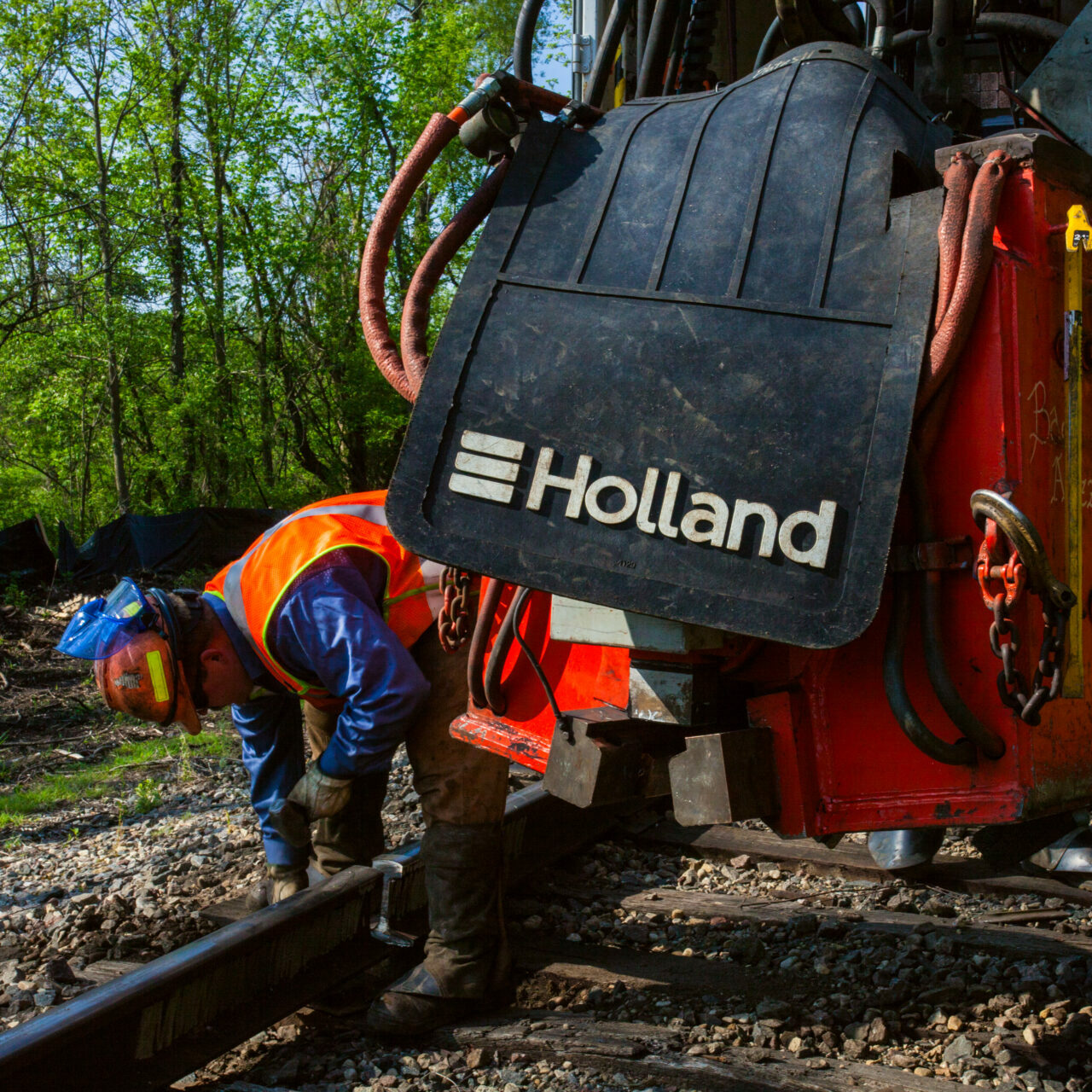
Repair Welding
Addressing the Essentials: Prioritize rail defects and bolted joints management to forge a robust and low-maintenance track structure.
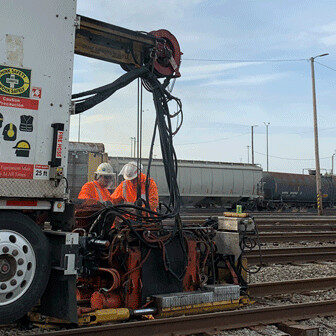
Short-Plug Repair Welding
Efficient and Nimble: Utilizing smaller teams and 5’ plugs, the short plug welding method uses less and equipment and leaves less scrap.
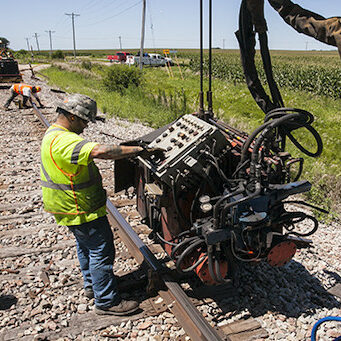
Joint Elimination
Strategic Conversions: Converting jointed rail to Continuous Welded Rail (CWR) decreases long-term maintenance expenditures.
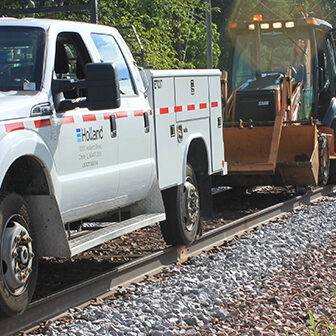
Rail Destressing
One-Step Process: Time, manpower, and needless temporary anchor/spike/ astener removal are eliminated, make correcting neutral rail temperature a one-step process..
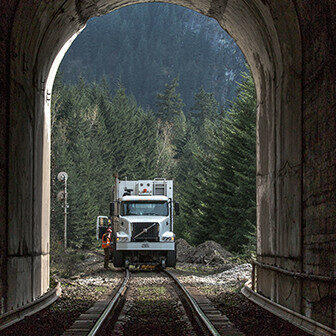
Closure Welding
Ideal Closure Solutions: Lower rail consumption reduces the amount of de-clipping and clipping required, improving productivity and reducing labor costs.
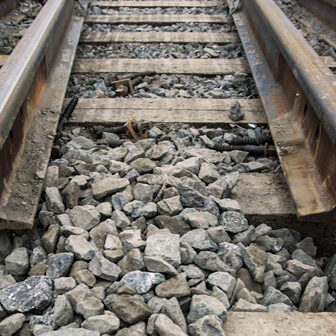
Turnout Welding
Extended Capabilities: Our equipment has the ability to weld on-track or from a right of way onto the track in order to flash-butt weld turnouts and more.